Gas Assisted Injection Molding was one of the fastest growing new injection molding technologies in the 1990’s. And yet, less than 20% of all currently active injection molding machines are equipped with this feature.
Here’s how Short Shot Gas Assist works:
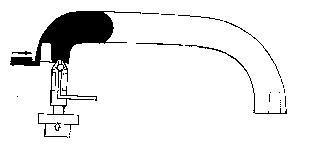
In the initial phase, the resin is injected into the empty mold cavity. The resin is coming in from the left of the article through an edge gate.
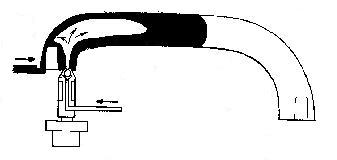
Gas injection begins as the resin injection continues thus preventing a hesitation of the flow front. The gas is injected through a special gas pin. The gas pin design and gas pressure have to work together to prevent plastic backflow.
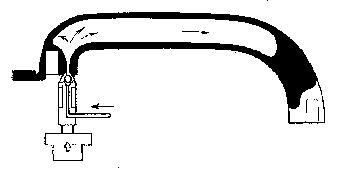
The resin shot is completely injected into the mold as gas injection continues. This gas injection keeps the flow front moving as the bubble forms inside the article thus stretching the skin to the end of the mold.
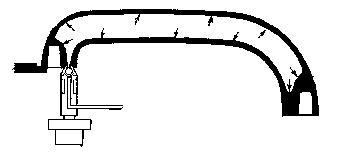
The material has completely filled the article, the skins are fully established, and the gas bubble continues to be pressurized thus creating an internal cushion to compensate for resin shrinkage.
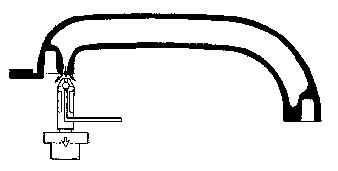
The article has cooled adequately to establish skin strength so the gas pressure can be vented. The gas must be vented prior to mold opening to avoid explosion. The gas pin retracts to accomplish this venting action.